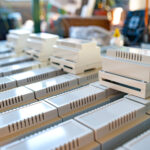
Powering Connectivity: Profine Plastic, Your Telecom Components Partner
03/02/2024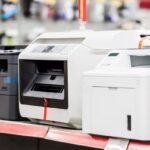
Enhancing Barcode Printers for Sato Malaysia Electronics
08/03/2025Plastic Injection Molding Success Story – Motorola Surveillance Systems
Motorola’s cutting-edge surveillance systems demand high-quality components that are both robust and precise. At the core of their designs are durable plastic housings and enclosures, essential for protecting sensitive electronics while withstanding harsh environments. However, achieving this level of quality while controlling production costs posed a challenge.
This plastic injection molding case study explores how we, as a reputable plastic injection moulding manufacturer in Malaysia collaborated with Motorola to meet their needs in the American market. By employing advanced mold designs and innovative injection molding techniques, we delivered superior components, reduced production cycle times by 18%, and achieved a remarkable 22% cost savings. This showcases how our plastic injection Malaysia expertise in injection molding for surveillance systems can result in measurable efficiency gains and cost reductions.
Key Takeaways for Industry Professionals
- Collaboration is Critical: Successful projects hinge on a strong partnership between manufacturers and clients, ensuring alignment on goals and expectations.
- Innovative Solutions Drive Results: Optimizing mold designs and employing cutting-edge injection molding techniques are pivotal for achieving efficiency and cost savings.
- Material Efficiency Matters: Strategic material selection not only reduces costs but also ensures long-term durability and performance.
- Precision Ensures Reliability: In industries like surveillance, precision manufacturing is non-negotiable for maintaining product integrity.
Overview of the Client & Project
About Motorola’s Surveillance Systems
Motorola is a global leader in surveillance technology, offering solutions designed for use in demanding environments. Their systems integrate advanced electronics that require reliable plastic enclosures to shield sensitive components from environmental stressors such as UV radiation, extreme temperatures, and physical impacts.
Project Goals
Motorola needed to address critical challenges in manufacturing these housings, including:
- Balancing cost reduction in injection molding with high durability standards.
- Creating components with intricate designs and precise dimensions for assembly efficiency.
- Meeting tight production schedules to align with new product launches.
Objective of the Collaboration: To deliver cost-effective, high-performance components for Motorola’s surveillance systems while maintaining quality standards and reducing production times.
Challenges Faced
Technical Challenges
The requirements for Motorola’s enclosures were highly specific:
- Precise Dimensional Accuracy: Essential to ensure components fit seamlessly with internal electronics, preventing operational issues.
- Material Durability: Needed to withstand UV exposure, temperature fluctuations, and physical impact without degradation over time.
- Complex Designs: The intricate geometries required precise mold engineering and production techniques.
Operational Challenges
- Material Efficiency: Motorola emphasized reducing material usage to lower costs without compromising structural integrity.
- Production Speed: Tight deadlines required efficient production cycles with no room for errors or delays.
Our Solution
To address Motorola’s unique requirements, we implemented a multifaceted approach focused on innovation, precision, and efficiency.
1. Innovative Mold Design and Advanced Injection Molding Techniques
Optimized Mold Design
- We developed custom molds with intricate detailing to meet the exact specifications of Motorola’s enclosures.
- Reduced material waste by creating molds that balanced structural integrity with cost efficiency.
Advanced Injection Molding Machinery
- Leveraged high-precision equipment to achieve consistent quality across production runs.
- Reduced production cycle times by 18% using automated systems to streamline processes.
2. Focus on Material Efficiency and Durability
Strategic Material Selection
- Identified high-performance thermoplastics capable of withstanding extreme conditions without compromising strength.
- Reduced material usage by 22% through optimizing component thickness while maintaining durability.
Ensuring Long-Term Reliability
- Tested materials to ensure they could endure environmental stresses, extending the lifespan of Motorola’s surveillance systems.
Challenge |
Solution |
Outcome |
Complex designs with tight tolerances | Optimized mold design for precision | Reliable assembly and system functionality |
Cost Pressures | Strategic material selection and efficiency | 22% cost reduction |
Tight Production deadlines | High-precision machinery and automation | 18% faster production cycles |
Results and Impact
Our collaboration with Motorola delivered impressive, data-driven outcomes that met all project goals.
Quantifiable Outcomes
- 18% Reduction in Production Cycle Time – Accelerated production ensured Motorola could meet product launch deadlines, improving operational efficiency.
- 22% Cost Savings – Efficient material usage and optimized processes resulted in substantial financial savings without compromising quality.
Product Performance
- Components exceeded industry standards for durability, maintaining performance under UV exposure, extreme temperatures, and physical impacts.
- Delivered long-lasting enclosures that ensured the reliability of Motorola’s surveillance systems in diverse environment
These results underscore how advanced injection molding for surveillance systems can balance cost-efficiency with premium quality.
Conclusion
By combining expertise, innovative techniques, and close collaboration, we helped Motorola overcome production challenges and achieve impressive results. This partnership highlights the potential of tailored solutions to deliver high-quality components, faster production times, and significant cost savings.
Are you looking for a plastic mold maker Malaysia partner to deliver cost-effective, high-performance injection molding solutions in the United States? Contact us today to explore how our expertise can support your next project and achieve measurable results.